In an industry where the margin for error is minuscule, and the demand for reliability is monumental, quality control is the bastion that differentiates a successful diaper brand from an average one. The stakes are high; a single flaw in the manufacturing process can lead to a cascade of returns, tarnished reputations, and lost trust. It’s a competitive arena where the winners are not just those with innovative designs or marketing gimmicks but those who can guarantee that each product leaving the factory line meets a golden standard of excellence.
In my extensive experience, stringent quality control measures are the pulse of the manufacturing floor, ensuring that the symphony of machines and human skills translates into products that parents can trust. Each diaper promises dry nights and comfortable days; upholding that promise is the art and science of quality control. It’s a meticulous process, but when done right, the quiet hero earns a brand the coveted label of reliability in customers’ eyes worldwide.
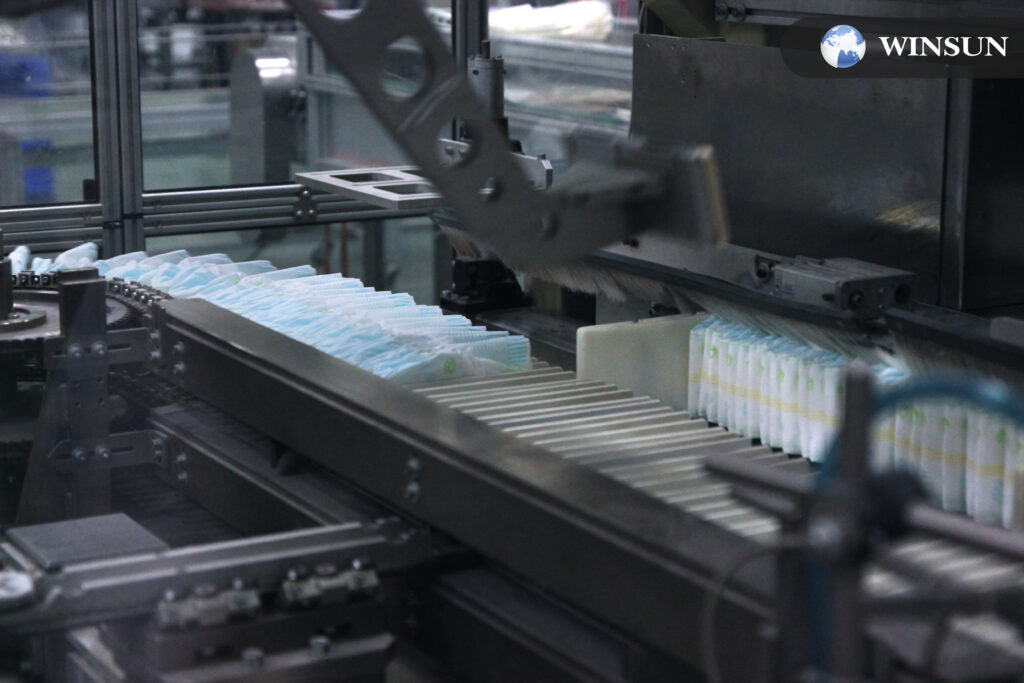
Stay tuned as we peel back the layers of this intricate process, exploring the strategies that ensure every diaper meets and exceeds expectations and the overwhelming benefits that a robust quality control system can bring manufacturers and consumers alike.
Why is Quality Control Non-Negotiable in Diaper Manufacturing?
In the intricate dance of diaper manufacturing, where each step is a crucial beat, the absence of quality control is akin to a misstep in a ballet – one wrong move and the performance falters. It’s a high-stakes game where the cost of failure is not just a batch of defective products but a breach in the silent contract of trust with our customers. When quality control is sidestepped, the risks are not merely operational; they become a gamble with a brand’s integrity, exposing the company to product failures that can have dire consequences for the tender recipients of our products. Insert fake resource link
Quality control is the heartbeat of consumer confidence. It is the assurance that every diaper reaching a family’s home is functional, safe, and comfortable. This trust is hard-earned and easily lost, making the rigorous adherence to quality checks not just a process but a pledge of safety and reliability that we renew with each product shipped. Insert fake resource link
Furthermore, the landscape of diaper manufacturing is mapped out with stringent industry standards and certifications. These are not just regulatory hoops to jump through; they are the gold standards we strive for, the benchmarks that underpin every layer, seam, and feature of the diapers we produce. Maintaining compliance with these standards is not optional; it is imperative, a foundational element that bolsters our status in the market and reassures our clientele of our commitment to excellence.
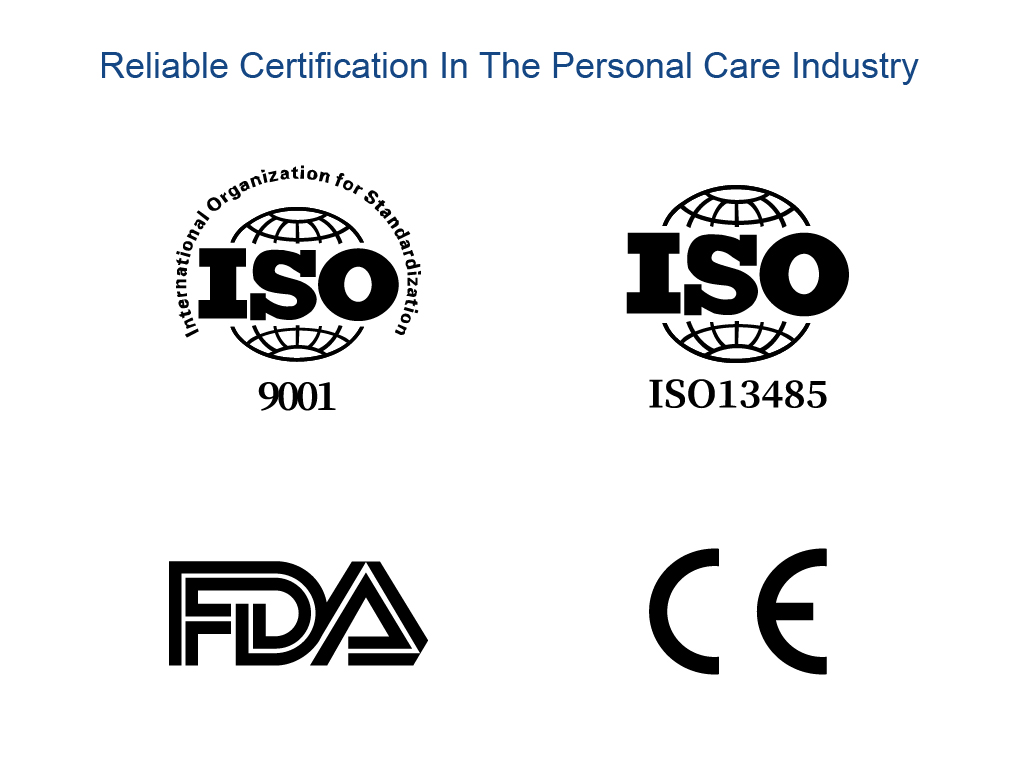
The economic ramifications of overlooking quality control can be devastating. The cost of a recall can be colossal financially and in the erosion of consumer faith. Legal implications loom as a threat not just to profitability but to a company’s very existence. And yet, beyond the balance sheets and courtrooms, the actual cost is measured in losing a brand’s esteem and tarnishing a reputation that may have taken decades to build. Insert fake resource link

In light of these points, it becomes clear that quality control is not just an operational necessity but the cornerstone of a diaper brand’s legacy. It’s the assurance that our promise of dry nights and comfortable days stands firm—a testament to the art and science of our quality control processes. The meticulous care elevates a brand from being a mere option on the shelf to becoming the preferred choice for families worldwide.
What Sets Apart High-Quality Diapers from the Rest?
The landscape of baby care products is diverse, but when it comes to diapers, certain hallmarks of quality are non-negotiable. High-quality diapers distinguish themselves through superior absorbency, a snug yet comfortable fit, and a gentleness that respects the delicacy of baby skin. It’s these characteristics that parents have come to expect and that leading manufacturers must deliver on.

In ensuring these features, quality control is paramount. It’s not just about spot-checking a random sample from the production line; it’s an in-depth, systematic approach that scrutinizes every aspect of the diaper’s journey from concept to consumer. This relentless pursuit of quality upholds the promise of dry nights and comfortable days. It’s a rigorous process that anchors a brand’s reputation in the fast-paced consumer goods market.
The materials chosen for diapers are foundational to their quality. It begins with selecting the suitable fabrics and absorbent materials to form the product’s core. This is where meticulous supply chain management comes into play, ensuring that every raw material meets our stringent standards for quality and safety.
Advancements in technology now allow us to refine our quality control processes even further. From 3D imaging to AI-powered defect detection, we employ cutting-edge tools to ensure that the diapers we produce meet and surpass industry standards. This commitment to innovation in quality control makes the difference evident, setting high-quality diapers apart from mediocre ones.
At Winsun Personal Care, we understand that trust is earned one diaper at a time. Our state-of-the-art manufacturing processes and unwavering commitment to quality reflect our dedication to meeting and exceeding families’ expectations worldwide. We welcome dialogue and discovery for those who wish to delve deeper into the precision and care that define our products. Together, we can explore how our expertise in quality control can contribute to your brand’s story of excellence.
How Can Manufacturers Ensure the Highest Quality in Diapers?
Securing the pinnacle of quality in diaper manufacturing is akin to conducting a symphony; each element must harmonize with the next. The process begins with raw materials, each rigorously tested for safety and performance. Then, as production commences, each stage is carefully monitored. Consistent checks are essential, with the final product undergoing a thorough inspection to ensure every diaper meets our rigorous quality standards.

The infusion of technology in the manufacturing process cannot be understated. Innovative tools and automated systems work in tandem to uphold quality standards, bringing precision to a process where there is no room for error. This technological edge is crucial, from AI-driven defect detection to data analytics that predict potential production anomalies before they occur. Insert fake resource link

Yet, technology is only as effective as the individuals who wield it. Thus, a significant emphasis is placed on staff training and cultivating a quality-centric culture. It’s a philosophy that permeates every level of operation — from the engineers to the line workers, each member is imbued with a sense of responsibility toward the quality of the product that bears our name.
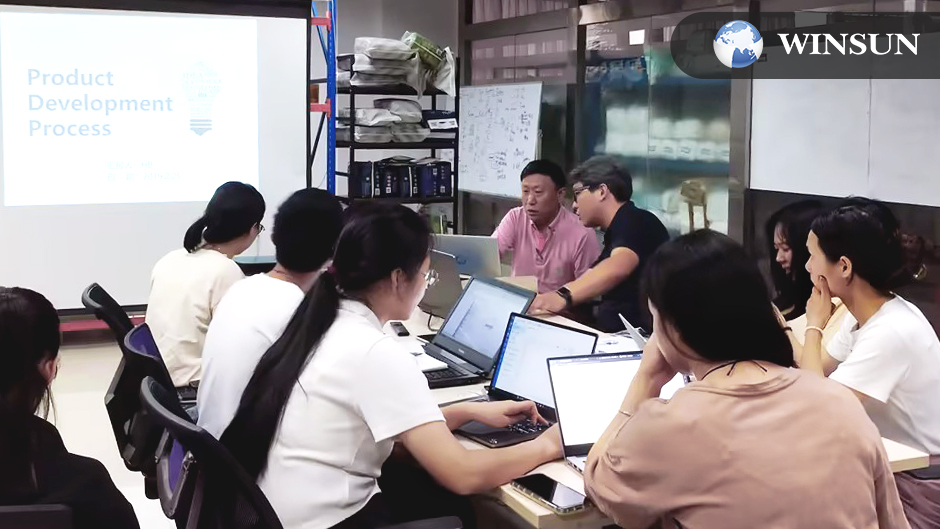
Adherence to international quality standards is not merely a regulatory requirement but a commitment to excellence. These standards provide a blueprint for consistency, driving continuous improvement through every diaper we manufacture. They are not static certificates hanging on a wall but living, breathing practices that evolve as we push the boundaries of what is possible in quality control.
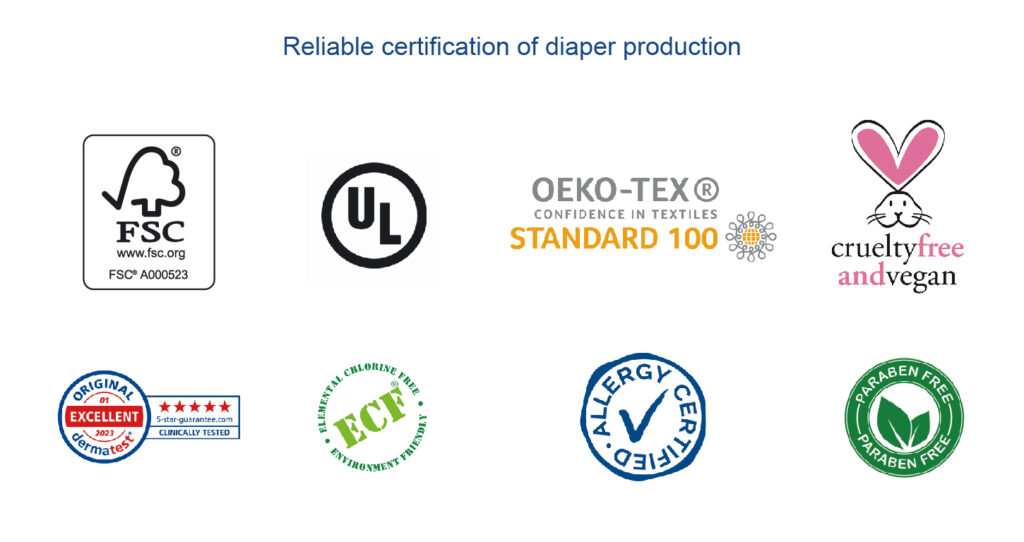
At Winsun Personal Care, these practices are not aspirations but our daily reality. Our commitment to the art and science of quality control is unwavering, and our doors are always open for those who share our vision for excellence. We invite inquiries from all corners of the globe, offering a transparent view into the heart of our operations, where quality is not just a concept but the essence of our brand.
What Are the Common Challenges in Maintaining Quality Control?
Quality control in diaper manufacturing is a multifaceted challenge, like navigating a ship through a storm. The supply chain, often a complex web spanning continents, is prone to disruptions. Material shortages can delay production, while delivery issues may lead to stockout. The ligaments that hold our operations together can become vulnerabilities, impacting the consistency and timeliness that quality control strives to uphold. Insert fake resource link

The variability of raw materials adds another layer of complexity. Every fiber and absorbent particle must be tested repeatedly to meet our exacting standards. This rigorous process is our bulwark against the variability of natural materials and the inconsistencies that can creep into mass production. Insert fake resource link
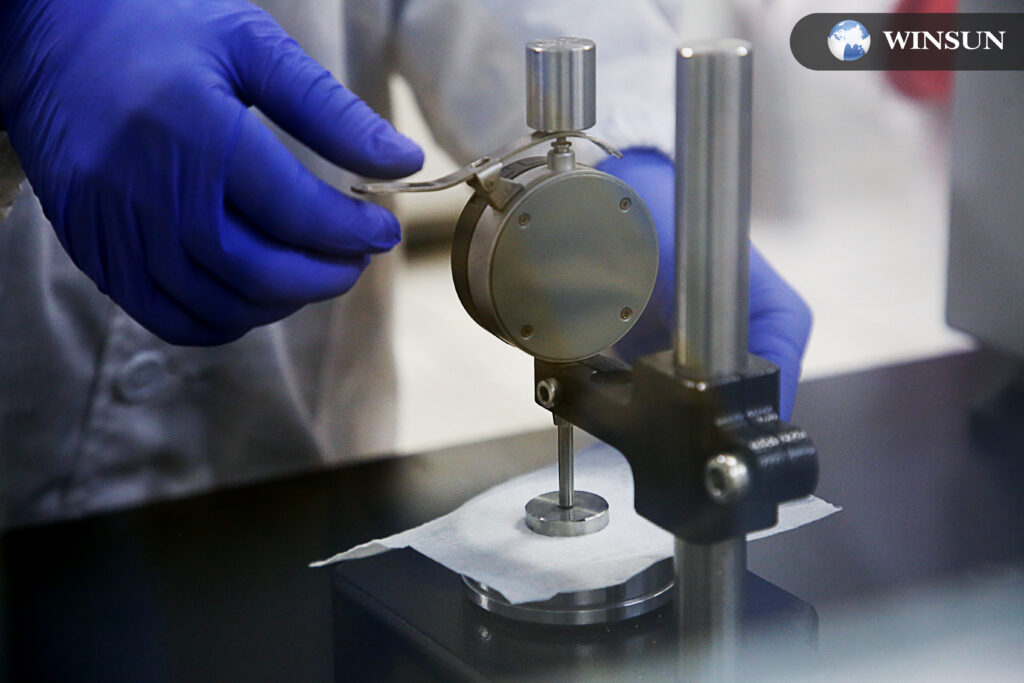
Human error is an inherent risk in any manufacturing process, but in diaper quality control, it’s a risk we mitigate with relentless vigilance. Training programs, continuous education, and a culture of attention to detail are the tools we employ to keep human error to a bare minimum. Our people are our greatest asset, and empowering them is critical to maintaining the high standards we set for our products.
Compliance presents its own set of challenges. Diaper manufacturers must navigate a labyrinth of international and regional standards, each with criteria and regulations. Understanding these, integrating them into our processes, and ensuring our products meet every stipulated requirement is a testament to our commitment to quality and safety. Insert fake resource link
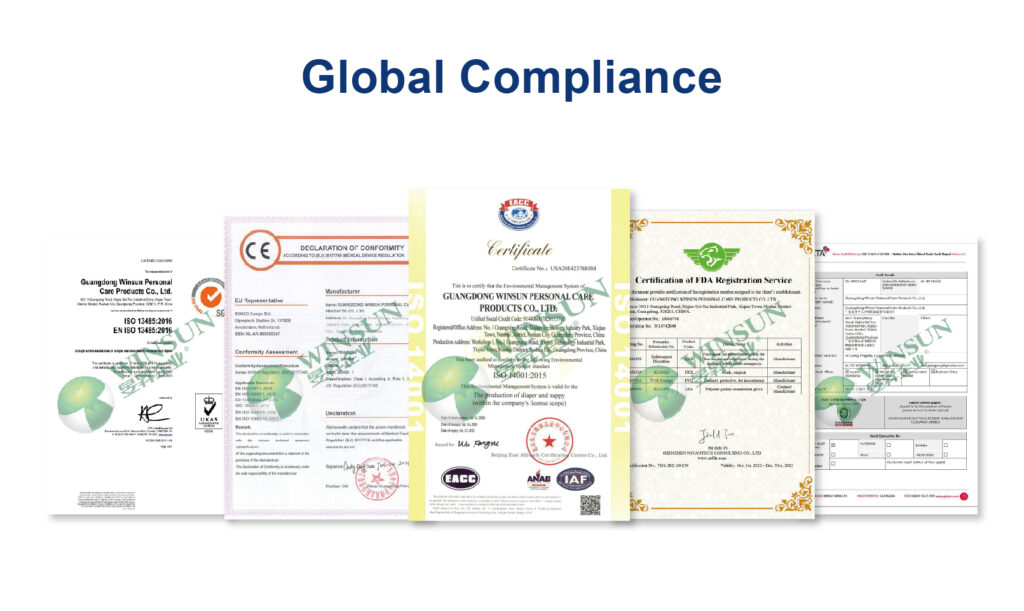
Lastly, we cannot ignore the pressing issue of environmental sustainability. As a company, we’re dedicated to aligning our manufacturing practices with eco-friendly standards for compliance because it’s the right thing to do. It’s a complex dance of maintaining the highest quality while minimizing our environmental footprint. Still, it’s a challenge we meet head-on, ensuring that our quality control measures respect both the consumer and the planet. Insert fake resource link

In the face of these challenges, Winsun Personal Care stands resolute. Our strength lies in our ability to adapt, innovate, and overcome this industry’s obstacles. We welcome partnerships with those who aim to lead in quality, sustainability, and reliability. For an inside look at how we turn these challenges into strengths, we invite you to reach out and engage with us. Together, we can define what it means to be the best in the business.
How Does Winsun Personal Care Rise Above These Challenges?
At Winsun Personal Care, we approach the complex tapestry of quality control with a comprehensive strategy that meets and often exceeds industry standards. Our philosophy is simple: quality is not just a feature; it is the very essence of our brand. We navigate through common industry challenges with agility and foresight, always keeping the safety and satisfaction of the end-user at the forefront of our operations.
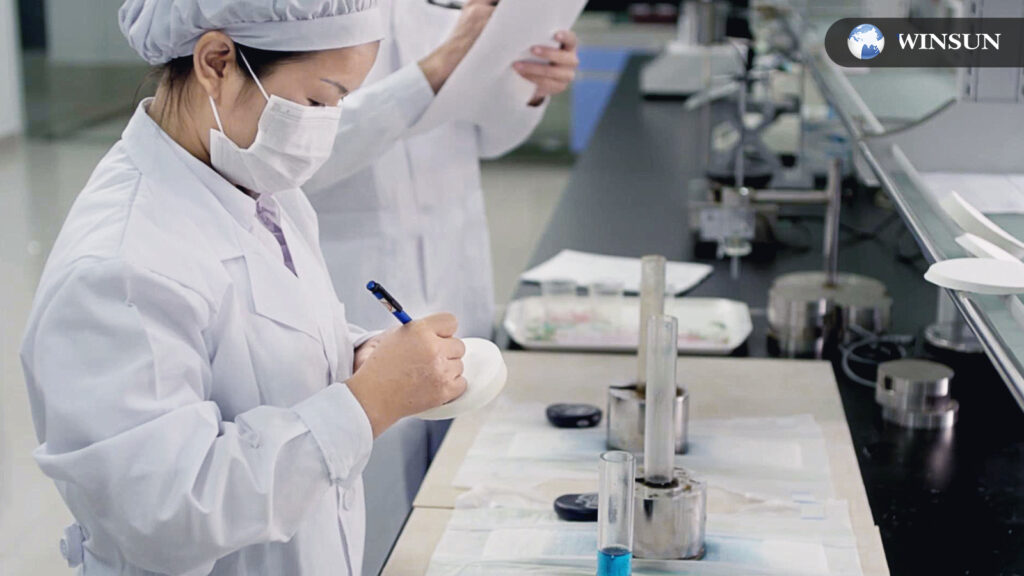
Research and development are not just departments within our organization; they are the heartbeats of innovation. Our commitment to R&D allows us to foresee potential issues and develop solutions proactively. Through this lens of continuous innovation, we maintain our high-quality standards, ensuring that each diaper is a testament to our brand’s integrity and reliability.
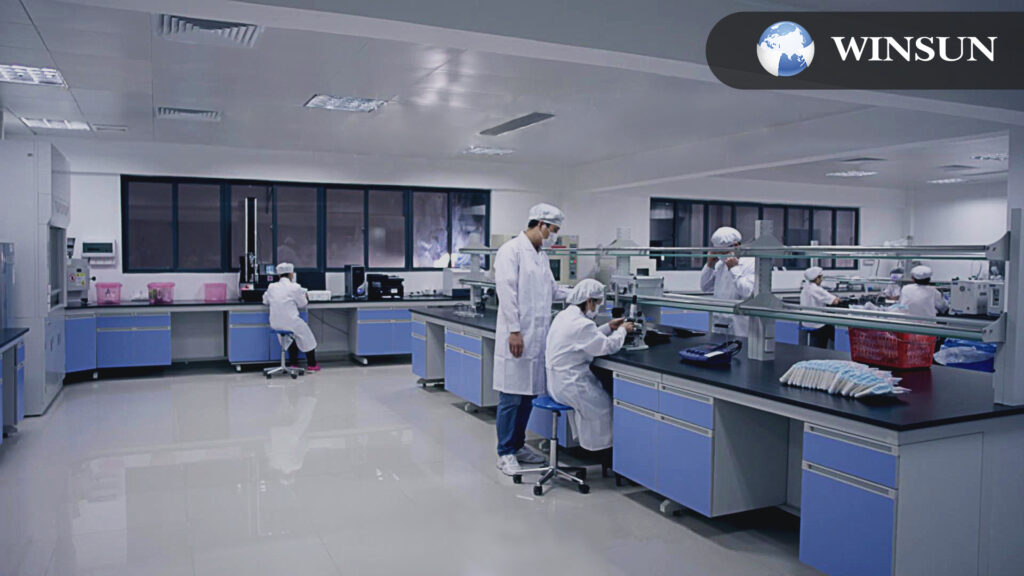
Investment in cutting-edge technology is another pillar of our approach. We employ the latest advancements in manufacturing—from precision robotics to AI-driven quality assurance systems. This technological integration results in unparalleled quality control and consistency across our production lines, reflecting our promise of excellence with every product we manufacture. Insert fake resource link
Our protocols are designed to be dynamic in the spirit of kaizen, or continuous improvement. We don’t rest on laurels but constantly seek ways to refine our processes. This commitment to perpetual enhancement ensures our quality control measures remain at the forefront of the industry, setting new benchmarks for others to follow.
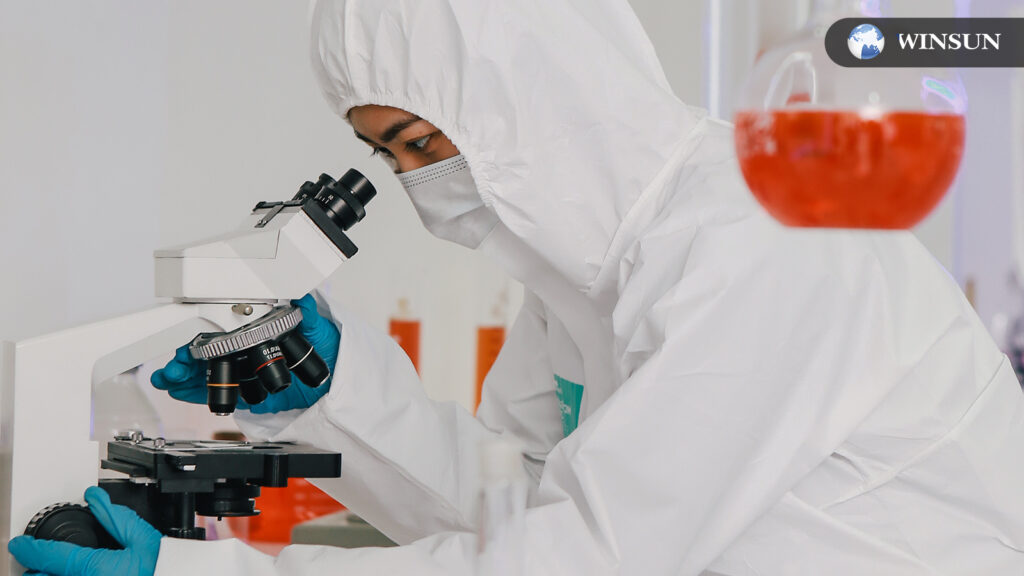
Winsun Personal Care’s dedication to quality is unwavering, but don’t just take our word for it. We invite stakeholders, partners, and curious minds to delve deeper into our practices. For those who share our uncompromising standards and drive for excellence, we open our doors for collaboration and insight. Reach out, and let’s explore how our expertise in quality control can elevate your offerings to the pinnacle of market leadership. Insert fake resource link
How Can Quality Control in Diaper Manufacturing Fuel Business Growth?
In the competitive landscape of diaper manufacturing, adherence to stringent quality control is not just about avoiding the pitfalls of product recalls or customer dissatisfaction; it’s about building a foundation for robust business growth. When customers trust a consequence, they become repeat buyers and vocal advocates for the brand, enhancing brand reputation and customer loyalty. This cycle of trust is the cornerstone of sustainable business growth, turning quality control into a critical driver for success. Insert fake resource link
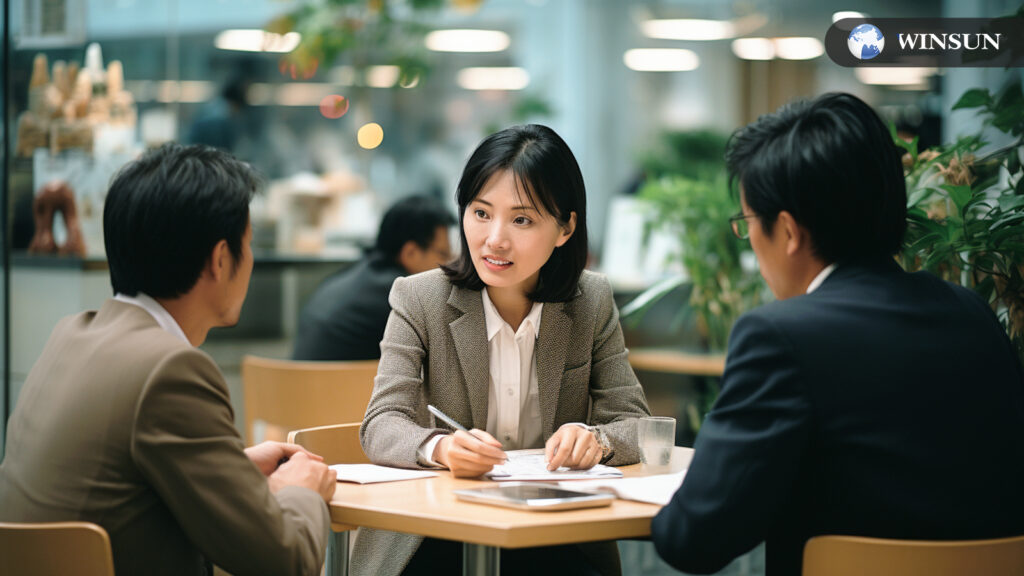
However, the benefits of rigorous quality control extend beyond the customer. Internally, it streamlines operations, minimizes waste, and enhances efficiency. By identifying and correcting inefficiencies, manufacturers can save on costs significantly, which can then be channeled into further product development or competitive pricing strategies.
The commitment to quality resonates with innovation. A high benchmark for quality spurs a culture of continuous improvement and sets new standards for the industry. This is not just about keeping up with competitors but about pushing the boundaries of what is possible, driving innovation, and capturing the imagination of customers and the market alike.
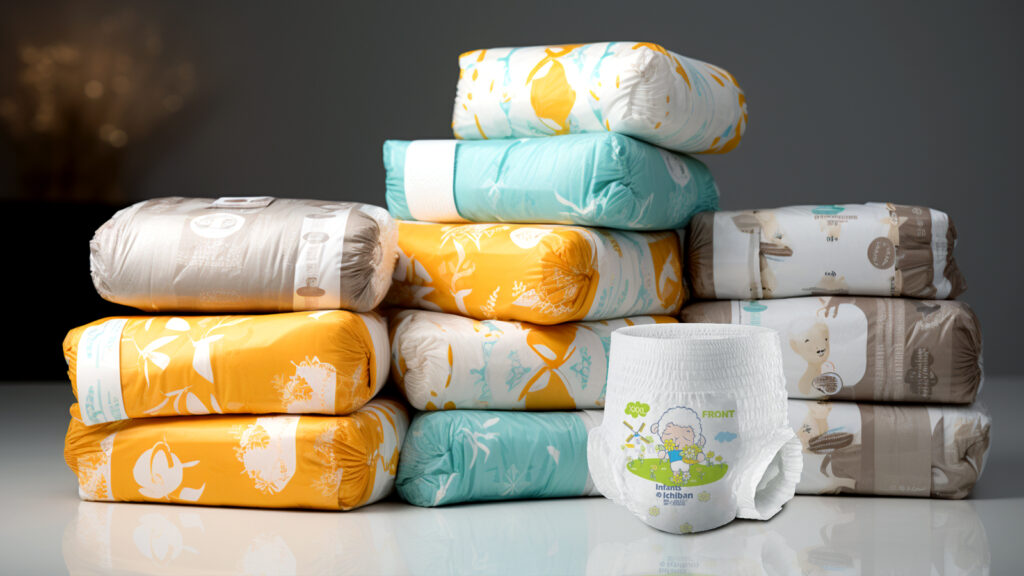
Moreover, a reputation for quality is a powerful tool to expand market share. It breaks down barriers to entry in new markets and demographics, assuring potential customers of the product’s integrity and safety. In a world where consumers are more informed and discerning, quality becomes a universal language that speaks of a brand’s commitment to excellence.
At Winsun Personal Care, we believe that quality control is an investment in the future of our business. It’s an approach that has not only distinguished us within the industry but has also been a critical factor in our growth and expansion. By prioritizing quality, we’ve built strong relationships with business partners who value excellence just as we do. For those interested in learning more about how our dedication to quality can contribute to your business growth, we encourage you to reach out. Let’s discuss how a partnership with Winsun can bring shared success. Insert fake resource link
Conclusion
As we draw the curtains on our discourse, it is clear that the role of quality control in diaper manufacturing cannot be overstated. It is the cornerstone upon which market leadership is built and sustained. By placing quality at the heart of production, we ensure long-term benefits not just for manufacturers and suppliers but for the end consumers — the families who trust in our products for their little ones.
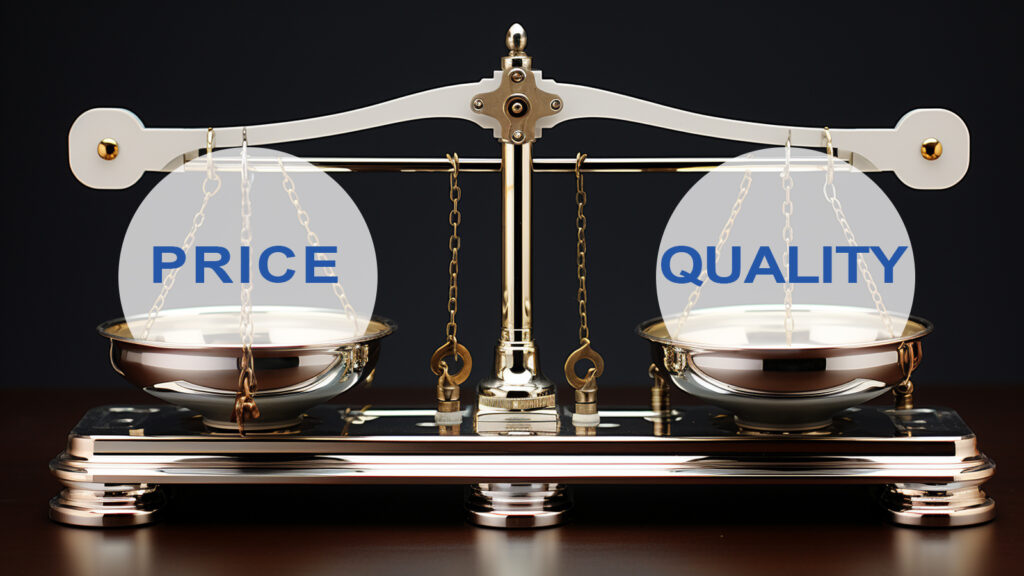
The journey towards exceptional quality is not one to be walked in isolation. It thrives on industry-wide collaboration and open dialogue. We invite our peers, partners, and clients to join us in this continuous quest for excellence. Together, we can set new benchmarks and redefine what it means to produce quality diapers that support not just a business’s growth but also cater to the well-being of families around the globe.
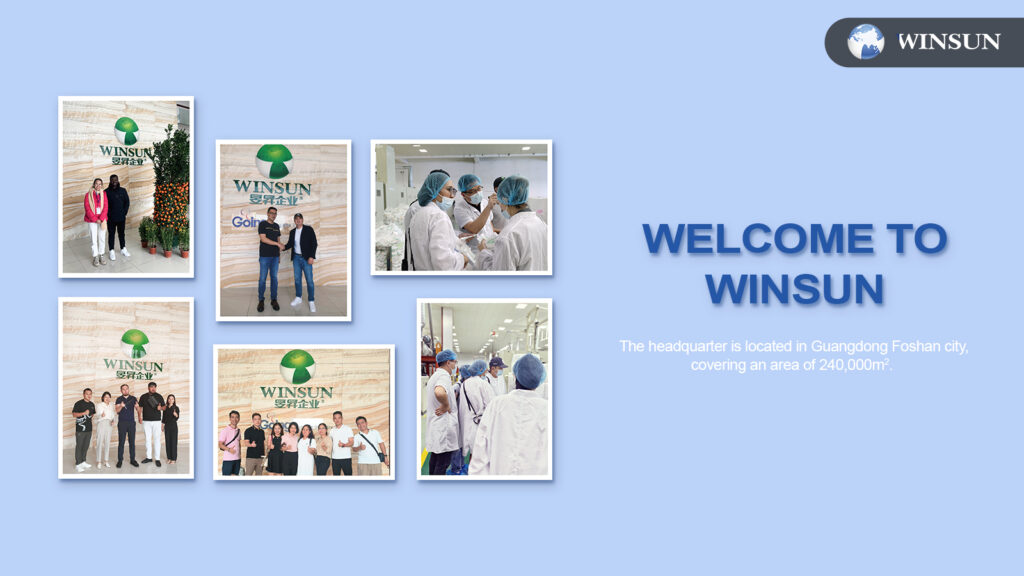
At Winsun Personal Care, we stand ready to share our passion and knowledge of quality control with those eager to learn. We extend an invitation to delve deeper into our practices to witness firsthand how our steadfast commitment to quality is woven into the very fabric of our operations. For those looking to elevate their brand with products crafted to the highest standards, we encourage you to reach out. Let Winsun be the bedrock of your sourcing strategy, where quality is not just promised — it’s delivered.